もくじ
- 第1部 基礎知識編
- 第2部 導入前準備編
- POINT15 WMS構築は全社的プロジェクトで
- POINT16 プロジェクト管理手法の活用
- POINT17 プロジェクトの進め方
- POINT18 WMS導入目的
- POINT19 ロジスティクスKPIを活用しよう
- POINT20 運用変更で解決するか、システム化で解決するか
- POINT21 システム化の範囲の絞り込み
- POINT22 得意先条件の調査
- POINT23 システムの拡張性の見きわめ
- POINT24 Auto-IDの活用
- POINT25 マテハン機器の活用
- POINT26 出荷作業の特性に応じた最適なツールの選定
- POINT27 要件定義書の作成
- POINT28 概算費用算出と費用対効果試算
- POINT29 RFPの作成
- POINT30 パッケージシステムか、独自のシステム構築か、クラウドか
- POINT31 物流のアウトソーシングとWMS構築主体の関係
- 第3部 業務改善編
- POINT32 改善プロジェクトの目的と目標の設定
- POINT33 現状分析に外せない「現地調査」
- POINT34 定性と定量の両面から現状実態を把握
- POINT35 定性分析で業務の構成要素やその関係性を明らかにする
- POINT36 インタビューに基づき「その場」で業務フローを作成する
- POINT37 オーダ分析1 出荷荷姿による作業方式と庫内レイアウトの検討
- POINT38 オーダ分析2 オーダ当たりの行数によるピッキング方式の検討
- POINT39 商品ABC分析1 保管方式とロケーション割り付けの検討
- POINT40 商品ABC分析2 業種に固有のロケーション割り付け
- POINT41 定量分析1 ワークサンプリング分析による改善対象の特定
- POINT42 定量分析2 ワークサンプリング分析の活用
- POINT43 物流ABCで改善効果の基礎データを作成
- POINT44 体系化により問題点と課題(取り組みテーマ)を明らかにする
- POINT45 標準化に対応した運用フローの作成
- POINT46 ボトルネックとクリティカルパス
- POINT47 基幹システム連携と運用フロー
- POINT48 標準化のための運用マニュアル作成
- POINT49 手待ち時間と歩行時間の削減
- POINT50 出庫、出荷作業動線の改善
- POINT51 在庫管理責任の明確化
- POINT52 適正在庫の考え方
- POINT53 保管形態、梱包資材の見直し
- POINT54 リードタイム短縮化への対応
- 第4部 システム連携編
- 第5部 WMSの機能活用編
- POINT67 WMSの基本機能
- POINT68 入荷予定データの活用
- POINT69 入荷検品
- POINT70 入荷実績データ作成と入庫指示書
- POINT71 入庫格納と入庫登録作業
- POINT72 フリーロケーションによる在庫管理
- POINT73 ステータス管理と振替機能
- POINT74 棚移動、ロケーション移動
- POINT75 棚卸
- POINT76 在庫調整
- POINT77 在庫照会
- POINT78 定期補充と緊急補充
- POINT79 出荷作業のバッチ組み
- POINT80 ロケーション在庫引当
- POINT81 出荷および出庫指示データの作成
- POINT82 シングル、トータル、マルチの3つのピッキング方式
- POINT83 流通加工
- POINT84 荷合わせ検品と積み込み検品
- POINT85 出荷停止とその解除
- POINT86 センター在庫の横持ち管理
- POINT87 ノー検品と伝票レスへの対応
- POINT88 緊急出荷、直送指示への対応
- POINT89 TC仕分けシステム
- POINT90 出荷先からの返品入荷
- POINT91 仕入先への返品出荷
- POINT92 締め処理と受け払い報告
- 第6部 導入効果の検証と見直し編
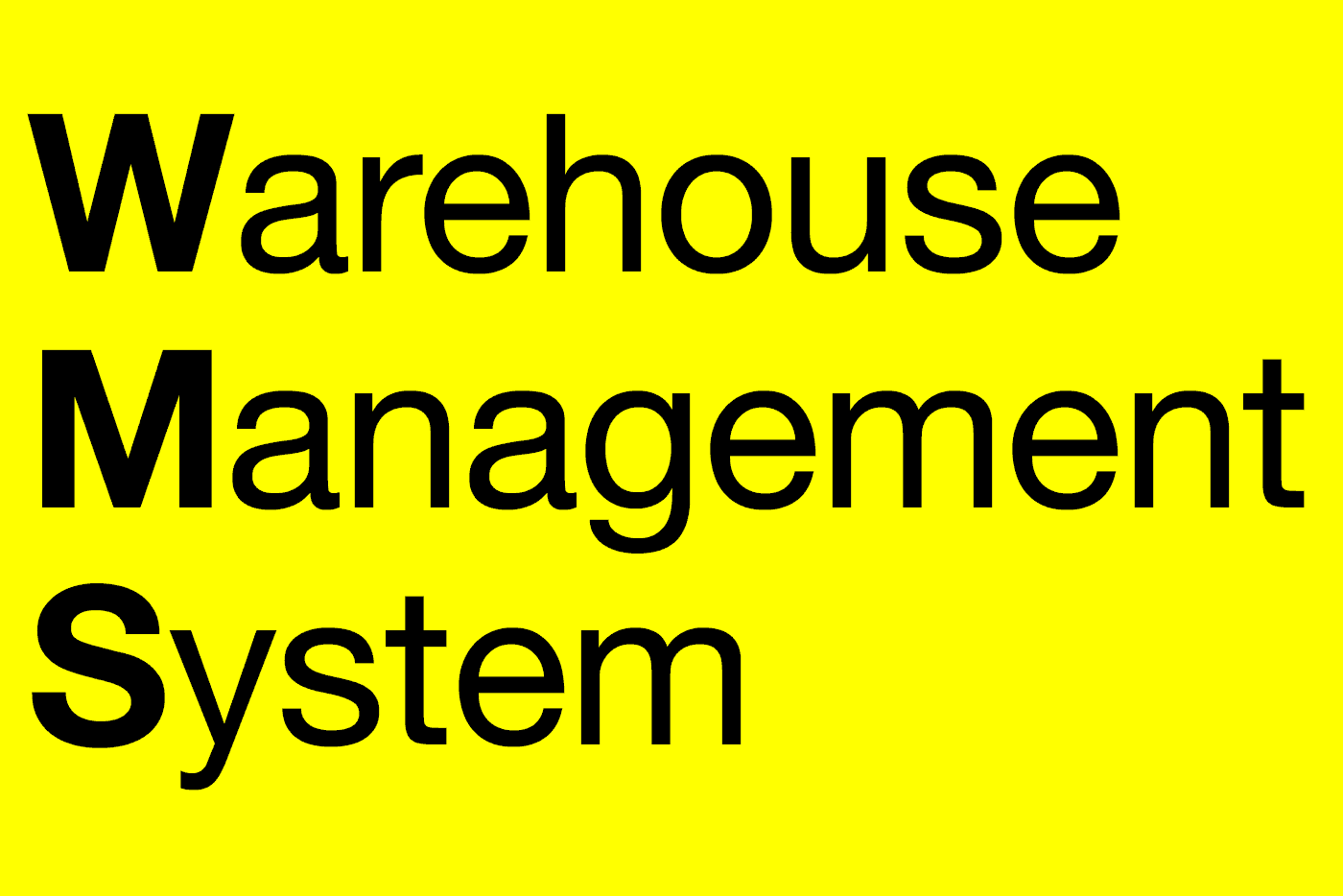
「図解入門ビジネス WMS導入と運用のための99の極意[第2版]」の要約メモ。
第1部 基礎知識編
POINT1 マネジメントツールとしてのWMS
WMS(Warehouse Management System)は倉庫管理システム。すべての作業を標準化することで、誰にでもできる作業に落とし込む。その上でボトルネックを取り除いて作業の流れを潤滑にする。
- 作業計画
入荷予定をもとに入庫作業計画をたて、出荷予定をもとに出庫作業計画をたてる。 - 作業進捗管理
エリア別、作業種別、出荷先別などの作業進捗をみながら、作業のボトルネックをみつける。 - 作業生産性
ハンディターミナルなどの端末を使用することで作業の精度をあげる。
POINT2 商物分離の原則
商流はお金の流れ、物流は物の流れ。商流は販売管理などの基幹システム、物流はWMSを中心とする物流管理システム。
商物分離の必要性は、コストとサービスレベルの適正化と、物流の情報に特化することで物流業務のアウトソーシング化が可能になること。物流の現場に、お金の管理伝票の作業を入れない。
POINT3 「見える化」のすすめ
倉庫内の作業実績や在庫管理情報をデータ化し、見える化を行う。作業生産性の悪化や品質低下の原因分析で、改善の方針を検討できる。納品遅延や欠品などがあぶりだされる。ゾーンやエリア別の、ボトルネックが見えてくる。
POINT4 現物在庫を管理するWMS
WMS導入の大きな目的は、QCD(Quality、Cost、Deliver)を向上させること。物流業務を効率化し、在庫精度を向上し、納期を遵守する。
POINT5 作業効率化を追求するWMS
ロケーションや棚番で紐付けを行い、ロケーション別在庫管理を行う。正確なロケーション管理によって、在庫差異が発生した場合も「いつ、どこで、どの作業でミスが発生したのか」を追うことができる。
POINT6 「在庫の見える化」で適正発注
適正な在庫を把握することで、需要予測数に調達リードタイムなどを考慮したタイムリーな発注不定期不定量が可能になる。
POINT7 物流サービス、品質向上への対応
トレーサビリティへの要求が高まっている。食品の安全性や不良品の追跡、商品に対する製物責任などを遂行するために、生産地やメーカーから消費者にいたるまで、すべての流通過程で追跡可能になることが要求される。
ロット、シリアル、製造年月日、賞味期限などの管理が要求されていて、物と情報の一体化が要される。しかし実現するには物流コストを上げてしまう要因になるので、WMSで作業実績を端末でデータ化するなど管理手法が求められる。
POINT8 通過型センターと在庫型センター
- 通過型センター(TC)
在庫保管を行わず、入荷した商品はすべて仕分け後に出荷する。 - 在庫型センター(DC)
商品の在庫管理機能を有する物流センター。 - 一括物流センターと専用センター
量販店やコンビニなどへ納品するセンター。効率的で定時納品を行うためにルート配送を行う。 - オムニチャネルセンター
BtoBとBtoCのWMSで運用する物流センター。ピッキング方式がBtoBとBtoCでは異なる。
POINT9 WMSの根幹機能となるロケーション在庫管理
ロケーション管理の階層には、倉庫、ゾーン、列・連・段、間口がある。
- 倉庫
倉庫ごとの特性に応じたロケーション管理。 - ゾーン
倉庫内のエリアを区切った「ゾーン」。 - 列・連・段
棚が並んだラインの単位を「列」、列の中の1つの棚を「連」、棚の各段を「段」と呼ぶ。 - 間口
段の中の区切りを「間口」と呼ぶ。ロケーションの最小単位。
POINT10 ロケーションの付番方法
ピッキングの進行方向にはワンウェイピッキングとジグザグピッキングがあり、どちらをとるかによって番号の振り方が異なる。
ロケーション番号は「3-3-2-3」など3,4桁にすることで、直感的にイメージできる。端末を使うためのロケーション番号のバーコードを貼っておく。
POINT11 固定ロケーションとフリーロケーション
センターの役割や目的によって、固定ロケーションとフリーロケーションを設定する。状況変化に柔軟に対応するために、固定とフリーを随時変更可能とする。
- 固定ロケーション
商品のロット管理や先入先出しの管理が不要な場合、頻繁にロケーションの見直しをする必要が内定番商品の管理に適している。 - フリーロケーション
商品の入荷日、ロット、賞味期限などの単位で、その都度格納したロケーションに登録する方法。回転率の高い商品の保管スペースを流動的かつ有効的に活用できる。
POINT12 ゾーン、エリアを活用した作業や商品への意味付け
- 固定ロケエリア運用例
入荷検品後は、指定されたロケーションに投入し入庫登録は行わない。 - フリーロケエリア運用例
入荷検品後は空いているロケーションを見つけて入庫登録を行う。 - 取引先別の保管エリアを設定する
出荷先別ピッキングで歩行距離を短縮化できる。 - 保管形態ごとにゾーン、エリアを区切る
パレットエリアとバラエリアを分けて管理する。フォークリフトとピッキングカートの作業など、作業性の違うものを分けることで効率化する。 - 返品、保留品、仮置きエリア
それぞれの商品ステータスに応じたゾーン、エリア管理。
POINT13 リザーブエリアとピッキングエリア
リザーブエリアは保管専用のエリア、ピッキングエリアは出庫作業だけを行うエリア。
POINT14 荷姿
入荷から出庫までにどのような荷姿で取り扱われるか確認する。入荷した商品を保管用に積み直す工数は極力減らす。たとえばパレットはパレットのままで棚入れを行う。ケースで入ってケースで出荷することがある商品は、できるだけケース荷姿のまま保管する。1つの商品で入荷から出荷までにケース、ボール、バラなど複数の荷姿を持つ場合、入り数や単位を間違わないように管理する荷姿の単位をそろえる。
第2部 導入前準備編
POINT15 WMS構築は全社的プロジェクトで
WMSはロジスティクス部門だけでなく、全社的なプロジェクトとしてスコープをたてる。
POINT16 プロジェクト管理手法の活用
PMBOKなどWBSの仕組みを使ってプロジェクトをコントロールしていく
POINT17 プロジェクトの進め方
リンクPOINT18 WMS導入目的
状況調査と課題整理、WMS導入目的の策定、要件定義、費用概算算出・費用対効果算出、RFP作成、システム開発、並行稼働と本稼働。
POINT19 ロジスティクスKPIを活用しよう
KPI(Key Performance Indicator)「重要業績評価指標」の指標をもとに、精神論ではない基準を設ける。
POINT20 運用変更で解決するか、システム化で解決するか
QCD「Quality(品質)、Cost(コスト)、Delivery(納期)」の観点をもとに、重複作業や無価値作業を洗い出す。ただ出力しているだけの帳票など。
POINT21 システム化の範囲の絞り込み
WMSの機能だからといって、すべての機能を使う必要はない。運用にマッチした最適なシステム化が必要。
POINT22 得意先条件の調査
- 納品時間
出荷先ごとの納品時間をもとにした、物流センターからの出荷時間を考慮して作業時間の組み立てを行う。 - 納品条件
納品時の指定梱包形態やラベル貼付、配送便の指定など。 - 納品率・欠品率
得意先の納品率や欠品率の基準に合わせて、物流センター内の在庫率や引き当ての優先順位を設定する。 - 誤出荷率
得意先の基準に適合するために、検品作業と手順を決め、定期的な誤出荷率の検出を行う。
POINT23 システムの拡張性の見きわめ
データ増大に対するシステムの拡張性は、WMS構築の重要な要件。マスタデータの増加、倉庫の増加、作業者の増加など。
POINT24 Auto-IDの活用
情報をバーコードなどに変換してスキャンすることで、自動認識を可能にする。JANコード、ITFコード(物流コード)、CODE39、QRコードなどの一次元コード。QRコード、RSSコードなどの二次元コード。ICチップなどのRFIDがある。
POINT25 マテハン機器の活用
マテリアル・ハンドリング機器の略称。パレット、カゴ車、コンテナ、DPS/DAS/GAS、ピッキングカート、フォークリフト、自動倉庫、音声/画像システム、ハンディターミナルなど。
POINT26 出荷作業の特性に応じた最適なツールの選定
- ピッキングシステム(掴み取り)
デジタルピッキング(DPS)は、作業者が視覚的に確認できるか検品機能がないため、誤出荷については弱みがある。ハンディピッキングは、画面確認作業が発生するので生産性は落ちるが、検品しながらピッキングするため、後工程での検品が不要になる。 - アソートシステム(種まき)
デジタルアソート(DAS)は、デジタル表示器の点灯でひと目で仕分け先がわかる。ハンディターミナル仕分けは、画面確認作業が発生するので生産性は落ちるが、検品まで同時に完了できる。
POINT27 要件定義書の作成
基本方針、システム化要件、品質要件、機能要件、現状改善フローと新業務フロー、運用要件、運用体制、スケジュール作成。
POINT28 概算費用算出と費用対効果試算
- 概算費用産出
要件定義にしたがって、多めに想定した費用の算出。 - 想定効果試算
定量効果と定性効果がある。定量効果は、各種削減できる費用など。定性効果は、その機能そのものでは金額を算定できなくても、定量効果を補強する効果。想定効果試算では定性効果を用いる。 - 費用対効果
その目的を達成するのにその費用は適正か、その費用は予想の範囲内か。
POINT29 RFPの作成
システム構築にとって必要な情報である、開発の目的や背景、機能、業務フロー、スケジュールなどの要件定義の内容をまとめたもの。
POINT30 パッケージシステムか、独自のシステム構築か、クラウドか
FIT&GAPの適合性、トータルコスト比較、機能の拡張性、運用変化に対する柔軟性、導入実績数や類似業種での実績など。
POINT31 物流のアウトソーシングとWMS構築主体の関係
物量の大きさ、センターでの運用の形態、企業規模などを総合して判断する。
第3部 業務改善編
POINT32 改善プロジェクトの目的と目標の設定
何のためのプロジェクトなのか、目的と目標の共有。
POINT33 現状分析に外せない「現地調査」
いつ、誰が、どんな仕事を、何のために、どんな頻度で、どんな手順で行なっているのか、そこではどんな問題が起こっているのか。
POINT34 定性と定量の両面から現状実態を把握
定性分析は外部と内部の数値化できない事象、定量分析は数値データをもとにした分析。
POINT35 定性分析で業務の構成要素やその関係性を明らかにする
いつ、誰が、どんな仕事を、何のために、どんな頻度で行なっているかを業務一覧表としてまとめたもの。
POINT36 インタビューに基づき「その場」で業務フローを作成する
持ち帰り作成せず、その場で業務フローを作成する。
POINT37 オーダ分析1 出荷荷姿による作業方式と庫内レイアウトの検討
どのような荷姿(パレット、ケース、バラ等)で出荷されるオーダーが多いのかを把握することで、作業や庫内レイアウトを検討することができる。
POINT38 オーダ分析2 オーダ当たりの行数によるピッキング方式の検討
シングルオーダーピッキング、マルチオーダーピックング、種まき方式、どの出荷方式を採用するべきかの検討。
POINT39 商品ABC分析1 保管方式とロケーション割り付けの検討
各商品を出荷頻度でABC分析することで、適切な保管方式とロケーション振り分けを検討できる。
POINT40 商品ABC分析2 業種に固有のロケーション割り付け
上位20%のアイテムで全体の80%の物量を占める場合や、80%のアイテムが1日1行しか出荷されていない場合など、ビジネスの特徴に合わせたロケーション割り付けを行う。
POINT41 定量分析1 ワークサンプリング分析による改善対象の特定
1つ1つの作業の大きさをとらえるためにワークサンプリング分析を行い、改善点を特定する。
POINT42 定量分析2 ワークサンプリング分析の活用
ワークサンプリング分析のために、まずは作業を要素に分解する。運搬や移動、仕分け、仕分け準備、リスト確認、リスト記入、商品確認、その他。
POINT43 物流ABCで改善効果の基礎データを作成
活動項目ごとの活動回数とコストから、活動ごとのコスト算出を行う。
POINT44 体系化により問題点と課題(取り組みテーマ)を明らかにする
定性分析と定量分析をもとに問題点を書き出す。問題点と要因をあきらかにする。
POINT45 標準化に対応した運用フローの作成
迷わない、探さない、歩かないを基本理念とする。専門性を排除して、誰にでもできる作業にする。判断が必要な作業を排除する。
POINT46 ボトルネックとクリティカルパス
ボトルネックは、ピッキング時に商品を探す作業や、出荷作業での梱包作業など。クリティカルパスは、バーコードを貼る作業や必要のない検品などの工程。
POINT47 基幹システム連携と運用フロー
出荷時間をもとに、基幹システム〜WMS〜作業の運用フローを構築する。
POINT48 標準化のための運用マニュアル作成
作業やルールの目的を意義を明確にする。
POINT49 手待ち時間と歩行時間の削減
全作業時間のうち、その90%が手持ち時間と歩行時間で占められている。
POINT50 出庫、出荷作業動線の改善
庫内作業での長い歩行時間や出荷の作業動線の長さは、ダイレクトに作業生産性に影響する。
POINT51 在庫管理責任の明確化
在庫管理への理解が異なる場合がある。仕入れ担当部署にとっての在庫管理は、在庫精度に対する責任はない。物流部門にとっての在庫管理は、在庫制度が求められる。
POINT52 適正在庫の考え方
適正在庫であることは、キャッシュフロー改善や物流コストの削減、企業経営の健全化にも直結する。
POINT53 保管形態、梱包資材の見直し
保管形態や梱包資材も定期的に見直す。
POINT54 リードタイム短縮化への対応
商品の保管期間を短くし、入荷待ち出荷をWMSでコントロールする。
第4部 システム連携編
POINT55 SCM構築におけるWMSの位置づけ
SCEは実行系のシステム。データ通信や物流センター、輸配送の業務を可動させるシステム。WMSはこのSCEに属する。
POINT56 TMSの目的と機能
WMSの目的は倉庫管理の効率化、品質向上、納品厳守であることに対して、TMSは輸配送の効率化、納品厳守、安全管理を目的としたシステム。
POINT57 取引先および外部システムとのデータ連携
ASN情報(入荷予定データ)、マスタ情報、返品予定データなどの連携を適切に行う。
POINT58 商品マスタ、商品コード管理の注意点
JANコードを基本として、インストアコードと呼ばれる社内コードと併用して管理する。さらに取引先コード、ITFコードなど物流コードなど複数登録して、WMSでは荷姿に応じて使い分ける。
POINT59 共通マスタとWMSとの関係
商流と物流の双方で使用するマスタは、管理項目や名称をあわせるために、基本的には基幹システムを主体として登録、メンテナンスを行う。
POINT60 WMS独自のマスタ管理
WMSに必要なマスタもある。出荷先ごとの配送コースや配送時間を設定する配送コースマスタ、配送コースや出荷時間ごとの作業指示のかたまりとなる出荷バッチ管理マスタ、梱包に使用する資材の種類と縦横高のサイズを登録した梱包マスタ、鮮度やロット管理のためのロケーションマスタ、ゾーンやエリアを管理するゾーン/エリア管理マスタ、ドラックを着けるためのスペースであるバース管理マスタなどがある。
POINT61 WMS独自のパラメーター
日付管理、商品特性や出荷先特性に応じた出荷条件など、WMSで独自に管理する項目をマスタに設定する。
POINT62 理論在庫と現物在庫
基幹システムで管理する帳簿上の在庫を理論在庫、物流情報システムで管理する現物の在庫を現物在庫を呼ぶ。整合性を取るのは、基幹システム側で伝票処理がすべて終わり、物流情報システム側ではすべての予定データの実績化が完了した時点。
POINT63 入荷予定と実績データ
基幹システムから送られてきた入荷予定データをもとに、WMSで入荷実績データを作成し基幹システムに返す。必要に応じて入庫実績データも基幹システムに送る。
POINT64 発注残、入荷残管理
発注残と入荷残データは、基幹システムの発注データのうちまだ入荷検品が行われていない入荷予定データの残データ。商流で作成した発注データを物流側で変更することはできないという商物分離の原則から、発注残、入荷残管理は基幹システムで行い、WMSでは入荷残管理を行わないのが基本ルール。
POINT65 出荷予定と実績データ
基幹システムから送られた出荷予定データをもとに、WMSで出荷実績データを作成し、基幹システムへ返す。必要に応じて出荷実績データも基幹システムに送る。
POINT66 受注残、出荷残管理
受注残は、基幹システムからWMSに送られてきた出荷予定データのうち、WMS側で現物欠品が発生、もしくはピッキングした際に欠品が判明して、そのまま出荷されずに残ったデータ。
第5部 WMSの機能活用編
POINT67 WMSの基本機能
WMSの機能は大きく分けて3つ。入荷、在庫、出荷、返品、印刷機能、照会機能、データ連携などのサーバ管理機能。入荷、在庫関連、出荷、返品などの検品機能。デジタルピッキングなどのマテハン機器連携機能。
POINT68 入荷予定データの活用
物流センターでの商品の管理制度は、入り口である入荷が重要で、後工程の在庫や出荷の制度に直結する。正しく商品を受け入れて適切なロケーション管理を行う。
POINT69 入荷検品
入荷予定リストは、作業に必要な最小限の情報をとりだす。入荷検品作業は、ハンディターミナルを使って、リストや現物のバーコードを活用する。
POINT70 入荷実績データ作成と入庫指示書
入庫検品作業が完了した段階で入荷実績データを作成する。
POINT71 入庫格納と入庫登録作業
入庫作業が終了したあと、商品を所定のロケーションに保管する入庫格納作業と入庫登録を行う。
POINT72 フリーロケーションによる在庫管理
フリーロケーションでロット管理などを実現できる一方で、固定ロケーションに比べて高い運用レベルが要求される。
POINT73 ステータス管理と振替機能
WMSでは、不良品など商品状態に応じたステータスを管理する機能が不可欠。このステータスを変更する機能を振替機能と呼ぶ。良品、不良品、保留品、破棄など。
POINT74 棚移動、ロケーション移動
商品の出荷頻度に応じて格納ロケーションを変更することで、出庫時の歩行距離の短縮化など、効率化を図れる。
POINT75 棚卸
会計上必要な期末棚卸と、在校状況を把握して運営を潤滑にするための循環棚卸の2種類がある。期末棚卸は、荷動きをすべて止めて正確な在庫数をカウントする。循環棚卸は、検証したい範囲を絞って行い、1日の作業終了後など空いた時間を利用して行う。
POINT76 在庫調整
WMSの在庫調整機能は、棚卸の際の在庫訂正とは異なり、一時的に差異調整すること。
POINT77 在庫照会
照会画面から条件を指定してデータを取り出せる機能も必要。
POINT78 定期補充と緊急補充
リザーブエリアと呼ばれる保管エリアから商品の出庫作業を行うピッキングエリアへの移動や、ケースエリアからバラエリアへの移動を補充と呼ぶ。定期補充は、朝昼夜など定期的に補充を行うこと。緊急補充は、ピッキングエリアの在庫が補充点数を切った時にリザーブエリアからの補充を指示する機能。
POINT79 出荷作業のバッチ組み
一定の出荷単位でデータを分割することで、その条件ごとに出荷作業を行う機能。配送ルートや納品時期に合わせた出荷指示データを作成し、出荷作業を効率化できる。
POINT80 ロケーション在庫引当
基幹システムから出荷指示データを受信後、WMSはロケーション在庫に対して引き当てを行い、出荷指示データを作成する。
POINT81 出荷および出庫指示データの作成
ロケーション在庫引当が完了したデータに対して、さらに作業者単位での作業指示データを作成する。作業方式やゾーン、出荷行数など、出庫作業の効率化を配慮した出庫指示データ作成が必要。
POINT82 シングル、トータル、マルチの3つのピッキング方式
シングルオーダーピッキング(摘み取り方式)は出荷先単位で商品をピッキングする作業方式。トータルピッキング(種まき方式)は、複数出荷先分の商品をまとめてピッキングして、その後出荷先別に仕分け作業を行う。マルチオーダーピッキングは、1回の歩行で複数の出荷先を同時にピッキングしながら仕分けも行う。
POINT83 流通加工
流通加工は、ギフトなどのセット品加工、値札印刷やラベル貼り、封筒入れ、組み立て、梱包作業、食品加工などの加工作業。
POINT84 荷合わせ検品と積み込み検品
センター内の各ゾーンやエリアから出庫された商品を、出荷先ごとに集めて検品する作業を荷合わせ検品と呼ぶ。
POINT85 出荷停止とその解除
商品の不良が判明した場合などの機能。
POINT86 センター在庫の横持ち管理
自社のセンター間で商品の移動を行うことをセンター在庫の横持ちと呼ぶ。
POINT87 ノー検品と伝票レスへの対応
ノー検品は、ASN情報により納品制度が担保されている場合に検品を行う必要がないこと。伝票レスは、ASN情報を活用して電子決済を行うこと。
POINT88 緊急出荷、直送指示への対応
基幹システムの出荷予定データにはない緊急出荷や、物流センターを通過させずに納品先に直送する例外処理もある。
POINT89 TC仕分けシステム
TCセンターのほとんどが、特定の小売業者の専用センター、一括物流センターであることから、TCセンターシステムとして標準化が難しい。
POINT90 出荷先からの返品入荷
商品出荷後に、得意先の都合や商品の破損によって商品がセンターに送り返されてきたものを得意先返品と呼ぶ。
POINT91 仕入先への返品出荷
仕入先からの誤入荷、過剰入荷、不良品などを仕入先へ返品することを返品出荷と呼ぶ。
POINT92 締め処理と受け払い報告
1日の作業が終了すると、日次締処理、更新処理、データバックアップなどをWMSで行う。
第6部 導入効果の検証と見直し編
POINT93 PDCAの継続
経営環境や物流を取り巻く状況は変化し続けている。
POINT94 実績データの分析
季節性の分析、カテゴリー分析などの出荷実績データの分析。出荷数量分析、出荷金額分析、出荷行数分析などのABC分析。
POINT95 定期的なロケーション、ゾーンの見直し
商品を出荷するまでの歩行距離は物流センターの中で最も大きな工程のひとつ。
POINT96 QCDの検証
効率化を追求するあまり作業品質の低下を招いていないかなど総合的な検証が必要。
POINT97 レイバーマネージメント
人のマネジメントは、特にコストに影響を与える重要な要素となる。
POINT98 現場力強化で継続改善
現場からの意見を吸い上げて、物流センター全体の運営に反映させることが、改善の継続のポイント。
POINT99 人材育成と教育の充実
管理職と作業者の教育を充実させることで、物流センター全体の作業生産性が向上する。